Fine woodworking is a craft that combines artistry with precision, turning raw wood into beautiful, functional pieces. Whether it’s building furniture, creating intricate carvings, or crafting custom cabinetry, the appeal of woodworking lies in its ability to blend creativity with skill. For many, the idea of having a personal woodworking shop at home is a dream—a space where they can unleash their creativity, build to their heart’s content, and have the freedom to work without interruption.
However, setting up a woodworking shop isn’t as simple as buying a few tools and finding a corner in your garage. Assuming you have the luxury of having a garage to set up this kind of space, collecting all the tools you may need may take a long time and a hefty investment depending on the type of work. For those new to the craft, the costs can add up quickly and it can be overwhelming. In this post, we’ll break down the true cost of starting a personal woodworking space and explore some more accessible and sustainable options.
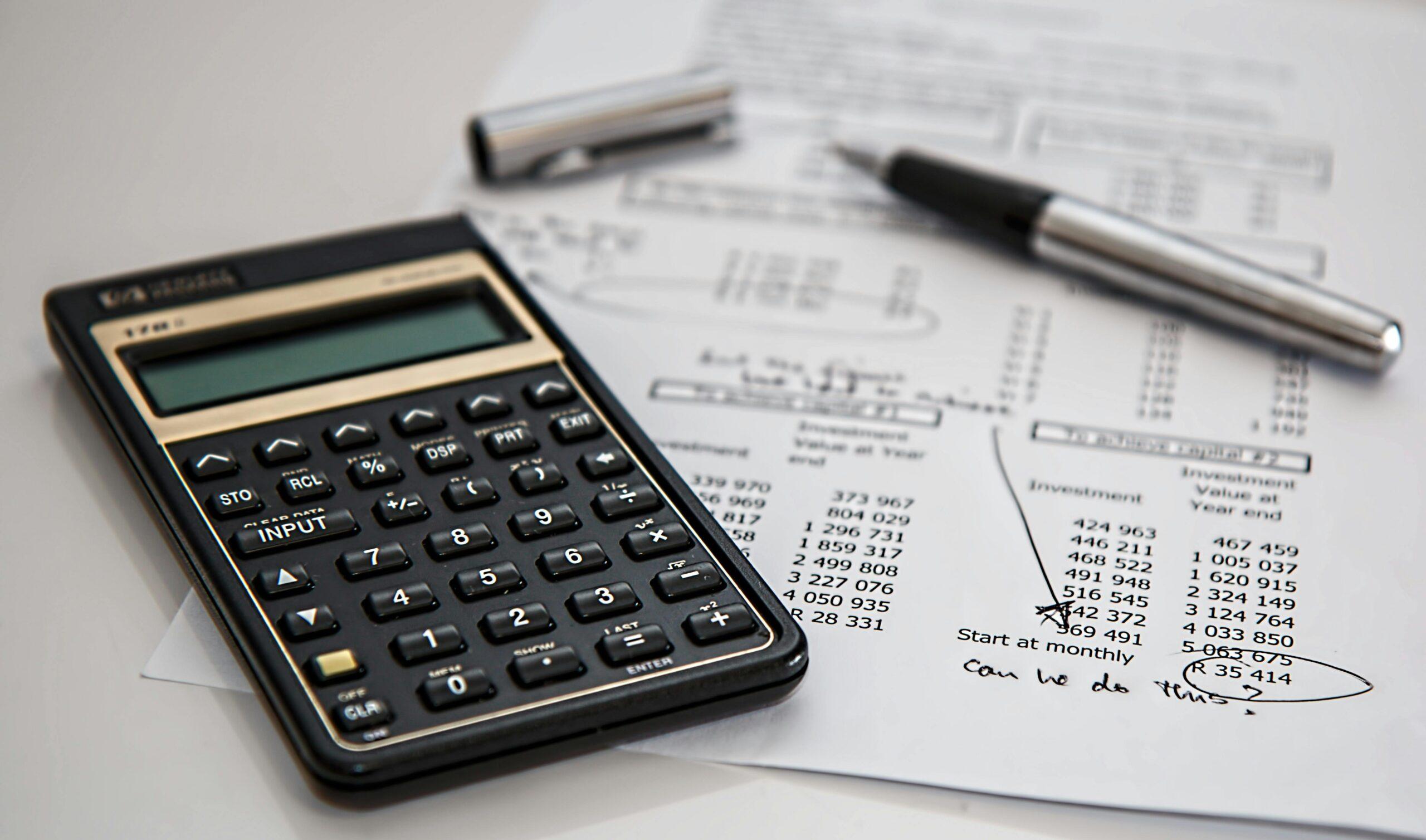
Initial Investment Costs
Tools and Equipment
The first step in setting up a woodworking shop is acquiring the essential tools. While the list can vary depending on the type of projects you want to undertake, some basics are necessary for almost any woodworking endeavor.
- Hand Tools: Chisels, hand planes, saws, and clamps are fundamental. A basic set of these can cost anywhere from $300 to $600, depending on the quality. Most glue-ups can require anywhere between 4-16 clamps if not more. You can never have enough clamps.
- Power Tools: An Impact Drill, Driver, Jig Saw, and Trim Router are essentials for anything from framing to fine woodworking. Battery powered sets usually cost more for the battery than the tool themselves and range anywhere between $100-300 per piece. You can save a bit by having corded versions, but those are much more rare these days. Make sure you stick with one brand for maximum compatibility.
- Machine Tools: These will take up the most space in your shop, but a table saw, miter saw, and drill press are staples in any woodworking shop. A mid-range table saw alone can cost around $600 to $2,000, while a safer professional sawstop ranges between $4,000-8,000. You might think you could make do with a jobsite saw which is much smaller, however you would be sacrificing a lot in both capacity and safety. What are you willing to save in cost vs safety with the number one most dangerous tool in a woodshop? Adding a miter saw, drill press, and a few other machine tools can push the total well into the the thousands if not tens of thousands.
- Dust Collection: Woodworking produces a lot of dust, which isn’t just messy—it can be harmful to your health and a major fire hazard. An appreciation for a clean shop is an absolute must to avoid long term health affects to your lungs and lowering your insurance costs. Shop vacs can handle most smaller tools, but if you are running large sanders, saws, planers, jointers, especially for long durations a good dust collection system can cost between $500 and $1,200 plus all the hose/piping to connect everything on top.
- Personal Protective Equipment (PPE): Safety is paramount in any woodworking shop. Safety glasses and ear muffs can be bought for under $50, but investing in quality gear may cost closer to $100. Don’t forget to protect your lungs from fine dust particles. Even a disposable mask is better than nothing, but a good reusable dust mask or respirator will last you years with replaceable cartidges.
Workspace Requirements
Woodworking requires space—not just for the tools but also for working on large pieces. You may be able to work with a typical single bay garage but the scale of your projects would be very limited. Some considerations include:
- Workbench: A sturdy workbench is essential and can cost between $200 to $1,000 depending on the size and quality. You can build your own, but materials alone may end up costing you about the same. They can make a great first project if you want to incorporate your storage and equipment into it though.
- Equipment: Every tool should have it’s own space for workflow. If not a permenant dedicated home, then a convenient storage location and somewhere to set it up when needed. Depending on what tools you have, this could end up taking up some pretty huge footprints. A table saw alone should have 8′ of in-feed and 8′ of outfeed to clear the blade on full size sheets. In many cases for fixed tools you need to have space for your material on either side. Even a 2-bay garage would be a tight fit for your essential machine tools.
- Storage: You’ll need storage for tools, materials, and finished pieces. Shelving and cabinets can add another $200 to $500. (Double that if you’re the type of person who likes to hoard pieces)
- Lighting and Ventilation: Proper lighting is crucial for precision work, and good ventilation is necessary for both comfort and safety. These upgrades can range from $300 to $1,000 but when it comes to your health and comfort you shouldn’t skimp. Nobody wants to work in an enviroment that is dark and covered in dust.
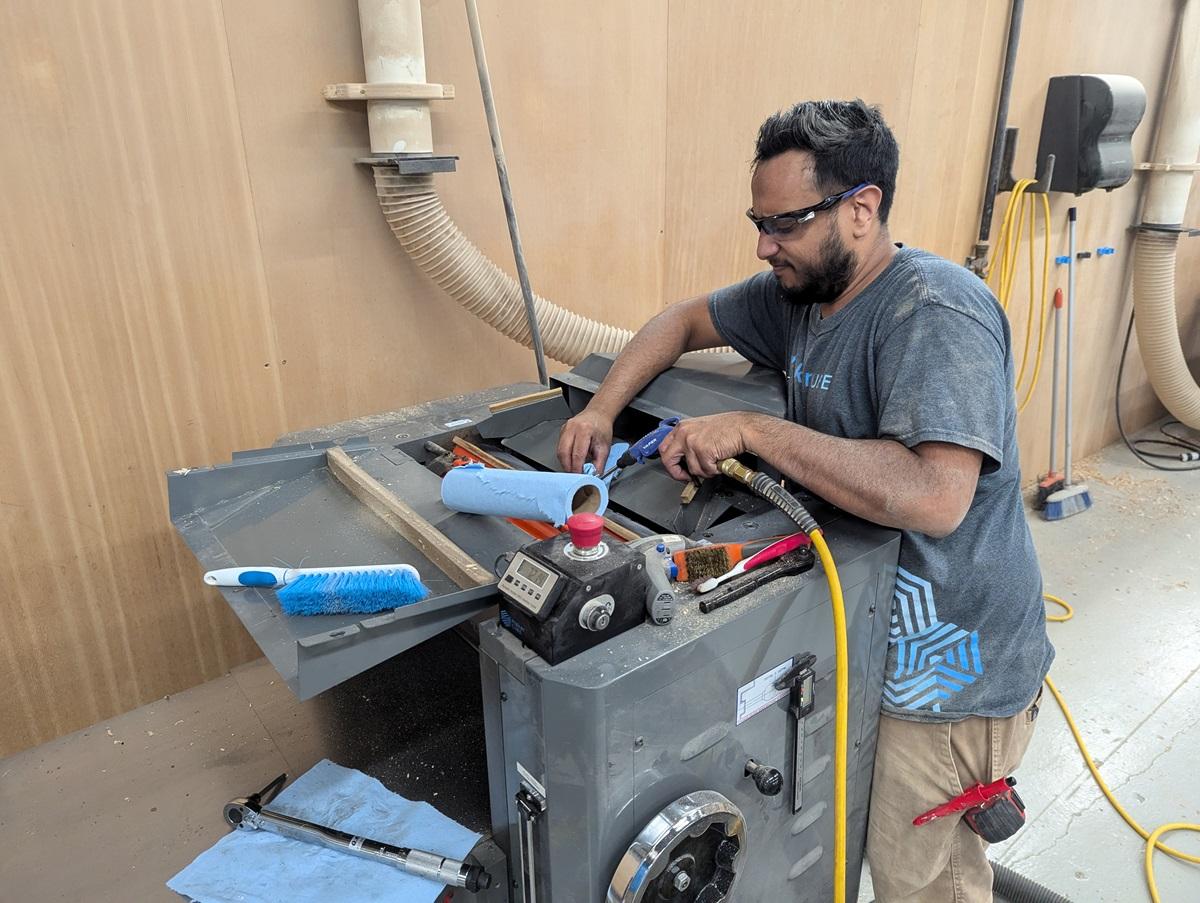
Ongoing Costs
Material Costs
Wood is expensive, especially high-quality hardwoods. Depending on your projects, you might spend anywhere from $200 to $1,000 or more on wood alone for a single project. Additionally, you’ll need to factor in the cost of finishing supplies like varnishes, stains, and sandpaper, and hardware which can add another $50 to $200 per project. Avoid using free materials with unknown origins. Pallet wood is the number one source of frustration when it comes to damaging your tools with hidden staples, stones, nails, and screws. While the material may be free, you’ll end up paying for it in tool damage and repairs. It also ends up being far more work to process and you can save yourself a lot of time and headache just working with new materials.
Maintenance and Repairs
Tools require regular maintenance to stay sharp and functional. Assuming you know how to maintain your own tools, sharpening blades, replacing parts, and general upkeep can cost $100 to $300 and a couple weekends annually. Additionally, unexpected repairs can quickly add to your expenses. General misuse will cause you to make those extra runs to homedepot to find replacements. If not regularly maintained the lack of any tool could set your project back until it’s fixed if you have no alternatives.
Utilities and Miscellaneous Expenses
Running power tools can significantly increase your electricity bill, especially if you’re working frequently. You might also need to consider heating or cooling your workspace, depending on your climate. If you want to make the most of a personal space, you don’t want temperature to be what keeps you out of the shop. As most personal shops are not usually well insulated (garages or sheds) the costs of heating or cooling can add another $50 to $100 per month to your regular utilities.
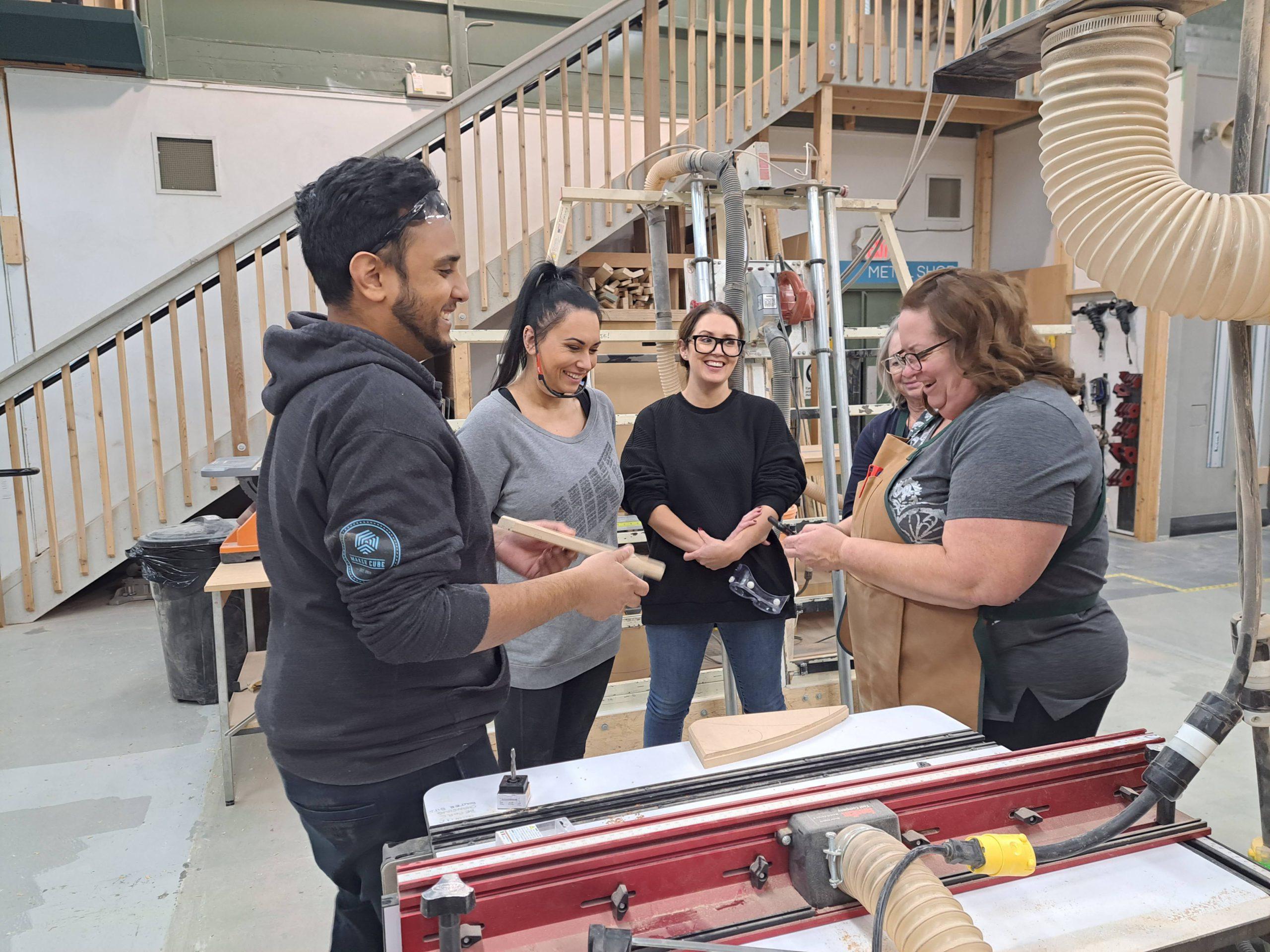
Time and Learning Investment
Skill Development
Woodworking is a skill that takes time to develop. You can cut a lot of the fustration at the beginning by taking some classes or workshops to give yourself a jump start. Even if the projects don’t align with your goals, there are always small tips, tricks, and techniques to add to your tool belt for the next project.
Mistakes and Waste
Many beginners find themselves making mistakes that result in wasted materials. Mis-cuts, poorly finished pieces, and trial-and-error can lead to wasted materials and time. This cost is hard to quantify but is an important consideration when calculating the total investment. Without the right expectations, this can be extremely discouraging. Don’t forget that making mistakes and exploring the process is part of the maker journey. We learn by doing and as long as you approach learning a new skill with that mentality consider these as investments towards your future abilities.
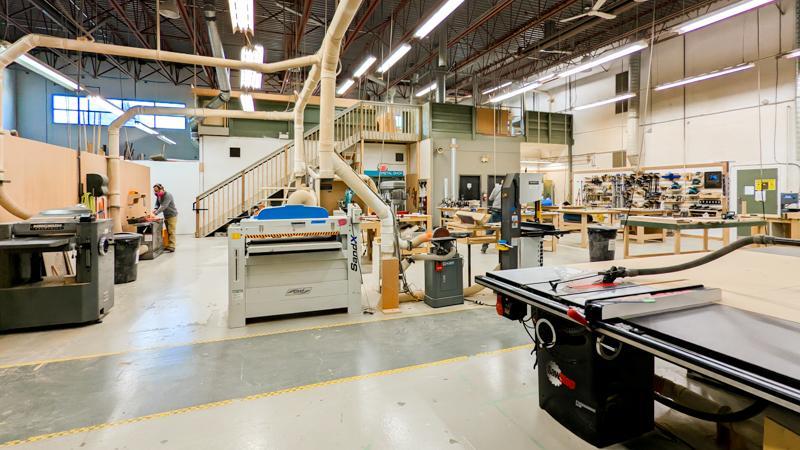
Personal Woodshop Alternatives
Check out your local community centers and maker spaces for a communal woodshop. While not totally ubiqutious every major city has at least one. The form these take can vary widly from small democratically run co-ops, to highly regulated city resources, to commercially run spaces like Maker Cube. You’ll have to weigh the pros and cons of each and how they will benefit your growth and help you acheive your goals.
Access to High-End Equipment
Commercially run workspaces like Maker Cube offer access to high-end tools and machines that would be prohibitively expensive to purchase for a personal shop. For example, not just one, but two professional-grade Sawstop table saws or CNC machine, each costing several thousand dollars, is available to members for a fraction of the cost. The capital investment to purchase one just of these machines could justify years of membership to access an entire shop of tools.
Regular Maintenance
Maker Cube regularly maintains all of it’s equipment. This means minimizing downtime on all tools so that when a member walks in, it’s ready to go for whatever project they want to do. This can be one of the biggest barriers for anyone to get their project started. Even if you have your own equipment at home, if it’s not set up, maintained and running smoothly the likelihood you’ll actually start your project the same day is pretty low.
Ample Space To Work
Communal spaces usually are much much larger than what anyone can afford at home. Our commecial woodshop is over 5000 sqft with additional 3000 sqft in other work areas for metal working, ceramics, 3D printing, painting and more. With multiple people sharing the same space, it makes it much more sustainable to access large work tables and open areas for even bigger projects. We even have rentable studio spaces and storage units for anyone who wants dedicated workspace or a place to put their materials.
Community and Collaboration
One of the most significant benefits of a communal workspace is the community. Being surrounded by other woodworkers means access to shared knowledge, advice, and collaboration opportunities. This environment can significantly accelerate your learning curve and reduce the likelihood of costly mistakes. Additionally, a community of makers is there to share the joys of a project coming together. Working in a communal space also has huge safety benefits with everyone looking out for each other. To avoid injuries and accidents it always helps to have an extra eye or someone you can ask for advice when you’re unsure.
Classes and Events
To complement the community is a plethora of classes and events. Every communal space offers many of these and Maker Cube is no exception. We run 4-6 classes a week to introduce our members to new skills, tools, and techniques. More than just a woodshop, we want to show our community that creativity and innovation comes from being exposed to a wide variety of experiences. Developing skills and proficiency comes from applying them and trying things out. Our classes are designed to always be hands-on, working with tools and walking away with something to show for it. Nothing makes a learning experience stick more than putting yourself in the moment and just doing it.
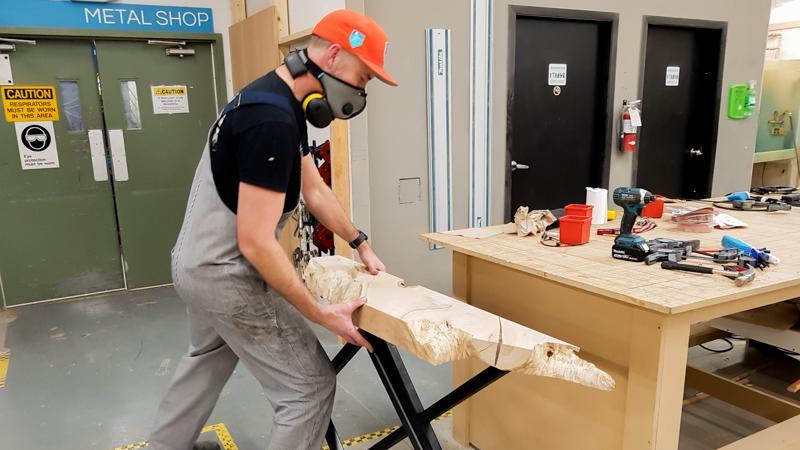
Conclusion
While the idea of having a personal woodworking shop at home is appealing, the reality is that the costs can be daunting, especially for those just starting. From the initial investment in tools and space to the ongoing expenses of materials and maintenance, the total cost can quickly add up. When you add up the costs of tools, materials, maintenance, and space, the price of setting up a personal woodworking shop can easily reach $5,000 to $10,000 or more.
Communal workspaces offer an affordable and practical alternative, providing access to high-quality equipment and a community of like-minded individuals. Whether you’re a seasoned woodworker or just beginning your journey, these shared spaces make the craft more accessible and enjoyable. A membership at a communal workspace typically costs anywhere from $60-200 hundred dollars per month, offering access to tools, space, and a supportive community without the massive upfront investment.
If you’re passionate about woodworking but unsure if you can afford to set up a personal shop, consider visiting Maker Cube. Our communal workspace offers everything you need to start creating, with flexible membership options and a vibrant community to support your growth. Come by for a tour or check out our upcoming workshops to see how you can get started!